What is rigid polyurethane foam?
Rigid polyurethane foam is made of isocyanate and polyether as the main raw materials, under the action of various additives such as foaming agents, catalysts, flame retardants, etc., mixed by special equipment, and high-pressure spraying. polymer. Polyurethane foam has two types: soft foam and rigid foam. Soft foam has an open-cell structure, while rigid foam has a closed-cell structure. Soft foam is divided into two types: skinning and non-skinning. The main function of flexible polyurethane foam is to cushion. Polyurethane flexible foam is often used in sound insulation linings such as mobile phone speakers, power modules, lampshade seals, automobiles, electronic equipment and computer communication equipment. Polyurethane rigid foam is a new type of synthetic material with waterproof function. It is mainly used in rigid support of structural parts, filling of design gaps, protective gaskets for sensitive devices, can withstand extreme environments, has durability and reliability, and is durable.
Foam plastic is one of the main varieties of polyurethane synthetic materials. Its main feature is porosity, so its relative density is small and its specific strength is high. According to different raw materials and formula changes, it can be made into soft, semi-rigid and rigid polyurethane foam, etc.; if classified according to the type of polyol used, it can be divided into polyester type, polyether type and castor oil. Polyurethane foam plastic, etc.; if classified according to the foaming method, there are block, molding and spray polyurethane foam plastic and other types. Polyurethane foam has a wide range of applications and penetrates into almost all sectors of the national economy. It is widely used in electronic equipment manufacturers, new energy industries and aerospace fields, and has become one of the indispensable materials. It has become one of the most widely used varieties in plastics.
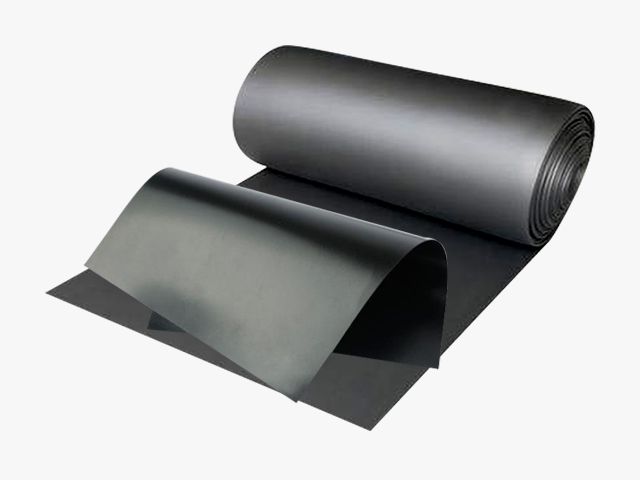
use:
1. High efficiency and energy saving, no gaps after filling, and strong bonding after curing.
2. It is shockproof and compressive, and will not crack, corrode, or fall off after curing.
3. With ultra-low temperature thermal conductivity, heat-resistance and heat preservation.
4. Efficient insulation, sound insulation, waterproof and moisture-proof after curing.
5. This caulk can be adhered to concrete, coatings, walls, wood and plastic surfaces.
General advantages of polyurethane materials: non-toxic and harmless
Wide range of hardness (Shore A15~Shore D90)
Higher load-carrying capacity than other elastomers at the same hardness
High abrasion and impact resistance
Wide rebound range
Suitable for high frequency deflection applications
Low temperature and good flexibility
Adopt special formula, stable at 140℃
Moisture Vapour Transfer - Suitable for Microporous Materials
Not affected by ozone erosion
Radiation resistant
Can be made into flame retardant material
Anti-fungal
High and low friction
Can be processed on standard equipment
Bonds to wood, metal and most plastics
Can be made into noise reduction material
Low molding and machining costs
Broad resistance to oils, greases and chemicals
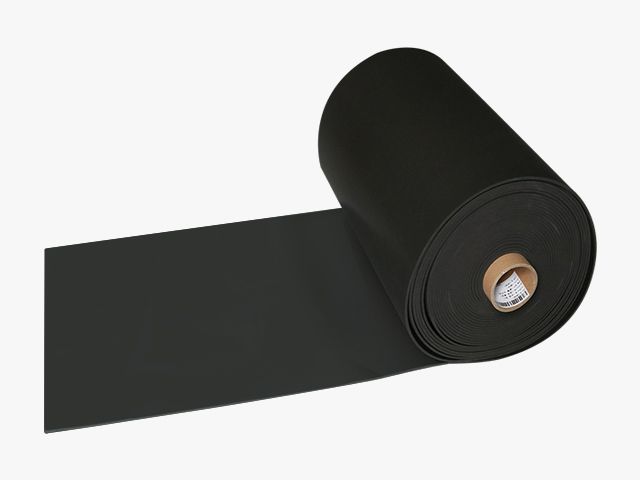